想要了解关于"饲料破碎料含粉率"的问题吗?不用犹豫,通过本文提供的信息,你将对此有更全面的认识。赶紧往下看吧,让我们一同揭开谜团。
含粉率和粉化率的区别
1、含粉率是指单位重量的颗粒/破碎料,经过一定目数的标准筛后,筛下物占样品重量的百分比。
2、而粉化率是指单位重量的颗粒或破碎料放在一种设备内,然后启动设备,一段时间后取出样品过筛,计算筛下物占样品重量的百分比。承受一定的外力作用后,变成粉的数量的多少,和颗粒耐久度相对应。也就是说颗粒耐久度+粉化率=100%。
3、含粉率低的饲料不一定粉化率就低。
颗粒饲料含粉率
猪料颗粒和牛料颗粒在含粉率制定上标准不一样,牛料一般比较恒定,1%左右,猪料根据阶段不同标准也不一样!
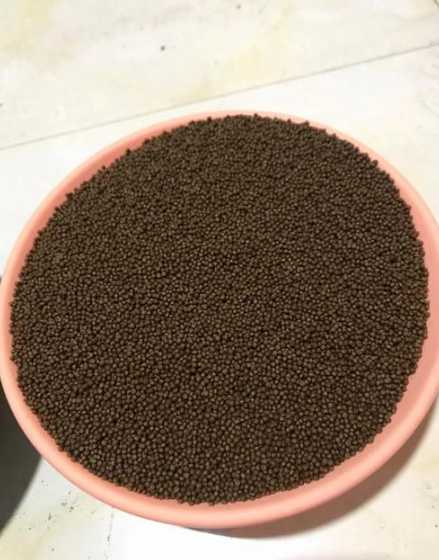
按照规定的来说一般颗粒料为2%;破碎料为4%,但实际上是很难做到的,主要看市场反应情况而定了!
含粉率:国标定义主要是指颗粒料,并且取样位置制定在冷却器处,标准筛为2.0mm等是有严格规定的,一般在5%以内;粉化率:取样位置是在成品仓库,不同的颗粒直径,要求有不同规格的标准筛筛分;一般在10%以内。
根据所喂动物品种的不同而有差异,一般猪料可在4%以内,鸭料必须控制在2%以下,鱼料不超过1%。否则将影响采食量和饲喂效果和浪费大。
关于饲料的含粉率
造成颗粒饲料粉化的因素很多,如原料的理化性质、粉碎粒度、制粒工艺及设备和冷却工艺等方面。 为了降低粉化率,也必须从这几个方面着手研究。一、原料的理化性质不同原料组成的饲料其制粒性能差异较大。玉米、豆粕含量较高的饲料(如小鸡料)制粒性能较好,粉料回流量少,成品成形率大都在95%上;而大糠、4粉含量较高的饲料(如通用料)则刚好相反,成品成形率仅90%左右,且经常堵塞环模,造成停产。 在不提高成本的前提下,在配方设计中应尽可能少用制粒性能差的原料。 1.淀粉含量较高的原料,在较高的温度和水分时调质,可促使淀粉糊化,制粒时可起润滑作用,提高制粒产量,同时颗粒冷却后粘结性好,粉化率低。 2.天然蛋白质的容量大,受热后变性,其可塑性与粘结性增大,破碎时产生的细粉料较少,有利于制粒产量的提高。 3.适量地添加油脂会使颗粒趋向软质化,减少通过环模的阻力,降低环模磨损的程度,增加制粒产量,但添加量不能超过3%。而添加糖蜜不仅可提高营养价值,也可做粘结剂使用,能提高饲料的耐磨性和硬度。 4.制粒性能特差的原料,可考虑适量添加一些胶结物,如淀粉质、木质素、明胶等,可以提高制粒粘结性,但是会加大成本。在制粒条件一定时(调质温度75~C,制粒机转速250r/min,制粒机电流150A,蒸汽压力0.22MPa),不同配方的饲料与粉料回流量有以下关系(感官鉴定以“+、++、+++、++++”表示回流量大小)。二、粉碎粒度粉碎的目的是为了后续工段更好地进行,同时也满足畜禽对饲料粒度的要求。国内外对饲料粒度与颗粒粉化率的影响做了大量的研究和试验。如图1所示,将同种组成的饲料进行颗粒化时,粒度越细粘结性越好,粉化率也就越低。诸多研究表明,粉碎粒度在0.4~0.6mm时,其制粒效果、电耗和粉化率都比较合理。三、重点加强对制粒工艺及其设备的管理 1.调质温度和蒸汽添加量淀粉的糊化需要三大要素:水分、温度与时间。当物料中水分含量相对稳定时,控制蒸汽添加量调节温度即成为关键因素。试验表明,随着蒸汽添加量的加大,颗粒的粉化率随之下降,这是物料中淀粉由于温度升高和水分增加,使其糊化加剧而提高了粘结性的结果。 蒸汽添加量过大会导致颗粒变形、水分过高及营养成分破坏加剧等一系列问题的出现。因此应适当控制,一般按产量的5%~6%添加,同样调质时间也应控制在15~30s。
如何提高饲料颗粒品质
饲料配方和原料品质对颗粒饲料质量影响极大。配方中含能量饲料、蛋白质饲料、矿物质饲料和添加剂预混料,分别为60%~70%、20%~25%、3%~5%、1%~2%。能量饲料和蛋白质饲料是主要组成成分,也是影响颗粒饲料质量的主要因素.
当前为了降低成本,各种替代原料越来越多,如麦麸、稻糠、DDG、啤酒糟、玉米蛋白粉、菌体蛋白、酵母、菜粕、棉粕、血粉、肉(骨)粉、蚕蛹粉等等。由于这些替代原料品质相差较大,致使原料吸收蒸汽的能力下降,表现为颗粒松散、表面无泽、硬度差、粉化率高。
为了改善颗粒质量,经常需要在配方中添加粘结成分,如小麦、次面粉、或膨润土等。根据我们使用的情况,加适量的小麦或次面粉效果较好,主要因其富含面筋蛋白和可溶性纤维素,较易于吸收蒸汽而熟化,从而提高颗粒质量。
蛋白质含量决定颗粒质量的重要因素,一般情况下,配方中蛋白质含量较高时,较易于制粒,颗粒质量也较好,因为蛋白质受热后可塑性、粘性增大,使制粒产量提高、质量好。
但当配方中蛋白质含量过高时,制粒效果下降。我厂1999年迫于竞争需要,对蛋鸡30%的浓缩料(除去玉米和面粉)进行制粒加工。其蛋白质含量在35%以上,由于配方中淀粉含量低,粗纤维含量12%以上,粗蛋白含量35%以上,因而,其吸收蒸汽能力严重降低,饲料调质温度仅为50~60℃,颗粒质量严重下降。
1.3纤维素含量饲料中粗纤维含量不宜超过10%,因为纤维自身的粘结力差,致使饲料粒子间的结合力下降,同时也影响饲料吸收蒸汽的能力。进而使饲料颗粒的硬度、形成率和产量降低,制粒设备磨损严重增大。
饲料中加入适量脂肪,则饲料通过模孔的流动性好,摩擦阻力减少,饲料易于成型,且制粒机环模磨损小,能耗低,颗粒质量好。但饲料中加入的脂肪过高,颗粒质量反而下降,因油脂可使饲料粒子间结合力下降,颗粒易破碎,贮存也困难。当饲料中需要过量脂肪时,可采用制粒后喷涂的方式添加。
一般情况下,饲料调质前的水分低于12.5%时,其吸收蒸汽的能力较强,调质温度高,颗粒质量好。根据多年的实践,粉状饲料调质后水分在15.5%~17%,效果好,按一般规律,粉状饲料调质时温度每升高10℃,水分约增加0.6%,而淀粉等糊化的温度要求在80℃,因而,淀粉饲料调质前的水分不宜过高,否则其吸收蒸汽能力下降,粉状饲料调质温度降低,饲料粒子间的粘结力下降,颗粒质量降低。
近几年来,每到新玉米上市时,饲料调质时添加蒸汽困难,制粒生产功耗高,生产率低,饲料颗粒硬度差,粉化率高。针对以上情况,我们采取粉状饲料暂存于制粒中间仓16~24小时使饲料粒间进行充分传质,然后再制粒,经生产考核发现,饲料吸收蒸汽能力上升,调质温度基本可保证在70℃以上。
粉状饲料中有吸湿性强的原料时,若生产准备时间长,则粉状饲料的流动性就会严重降低,同时,这类饲料制粒性能差,颗粒质量差。
例如,在生产乳猪料时,加入柠檬酸乳清粉、代乳粉等原料,由于这些原料遇空气后极易变粘稠,且遇高温易焦化,制粒时加蒸汽特别困难,调质温度低,颗粒质量差。生产这类饲料时,只能采用少加蒸汽快速生产法。
饲料含粉率国家标准
饲料含粉率国家标准,以下是对其的详细解释:
3.标准筛筛孔径为2.0mm,含粉率一般在5%以内。
4.粉化率取样位置在成品仓库,不同的颗粒直径要求不同规格的标准筛筛分,含粉率一般在10%以内。
5.猪料含粉率一般在4%以内,鸭料必须控制在2%以下,鱼料不超过1%。
以上是饲料含粉率国家标准的详细信息,希望对您有所帮助。
文章到此结束,如果本次分享的饲料破碎料含粉率和饲料含粉率国家标准的问题解决了您的问题,那么我们由衷的感到高兴!
标签: 饲料,破碎